Uptime is the only time that matters!
SURE-thing Inspection Solutions
Capable of monitoring 800 containers per minute.
Are errors in your manufacturing process costing your company a lot of money? Without an inspection system, even the most efficient processes have the potential for mistakes. Whether it’s testing the quality of an item, inspecting food or beverages for safety, or simply examining a product’s weight, size or shape, IPM will work with your team to implement the right vision system for your business. We can help you eliminate the possibility of the wrong product ending up in the wrong package!
Benefits of Vision Inspection Systems
Every product defect that occurs as a result of the manufacturing process wastes materials and cuts into the overall conveyor system.
. Automated inspection systems utilize cameras for data collection and computer software that provide data analysis to help reduce these unwanted costs. Product inspection and testing is a key element to most manufacturing processes. All systems are designed to help enhance efficiency and effectiveness of yourIn addition to increasing profits, some additional benefits to inspection systems are listed below.
- They can provide a consistent overview of the production line, identifying and classifying defects for future reference.
- They adapt, quickly and easily, to different product types and surfaces and can be adjusted to accommodate changes in product lines.
- They can be programmed and monitored remotely and can inspect products more effectively and efficiently than humans can.
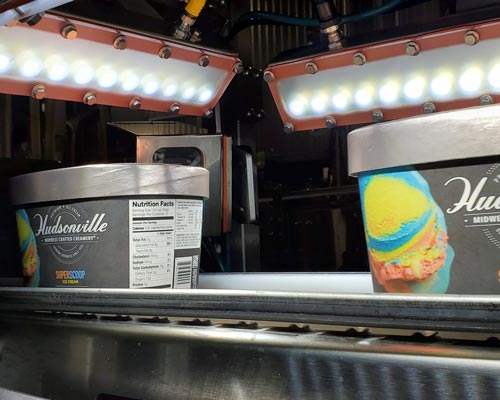
UPTIME IS THE ONLY TIME THAT MATTERS!
Vision Inspection System
Why Choose IPM?
IPM quality control inspection systems use barcode readers including side view cameras, overhead cameras, remote control panel, and an automatic reject system. The position and number of cameras implemented is designed for system redundancy. This means each barcode gets read at least twice as it travels through the inspection zone, minimizing false-positive rejections. If the wrong barcode or misread (no read) is detected, the system could automatically push the questionable product into a manual inspection bin.